Reduce VOC’s in Automotive-Seating Molding Operations
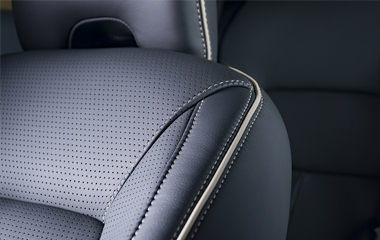
Cosolvents are “substances added to a primary solvent in small amounts to increase the solubility of a poorly-soluble compound”[1]. Hightower Products has developed their cosolvent technology in response to a growing shift from solvent-based mold release to water-based mold release. Through decades of research, the SA-Series was developed as Hightower Products’ co-solvent mold release for polyurethane molding.
Polyurethane manufacturing is a broad industry that is made up of numerous processes such as cast elastomer, integral skin, rigid foam, flexible foam, and high-resilience foam (Automotive Seating). The Hightower SA-Series was specifically developed as a solvent-alternative release agent for use in automotive seating applications.
Automotive Seating is a difficult process that historically has been released via the use of a solvent-based mold release. Hydrocarbon-based solvents are utilized in these systems to disperse high-melt polymers. The solvent release agent is then applied to the mold surface prior to the polyurethane foam being added to the mold. This leaves a uniform coating on the mold surface which prevents the polyurethane from sticking to it. The advantage of a solvent-based system is that it allows for the manipulation of the “dry time” (time between application of the mold release and the introduction of the PU system). Shortening the dry time can be done by formulating with faster drying solvents that evaporate at very low temperatures. These properties that make solvent-based mold release easy to use are the same properties that are receiving negative attention in the industry today. The solvents used in these release agents are typically classified as Volatile Organic Compounds (VOCs). Volatile Organic Compounds (VOCs) are “organic chemical compounds whose composition makes it possible for them to evaporate under normal indoor atmospheric conditions”[2]. In recent years governmental regulation has pushed for the reduction in VOC emissions by manufacturers. VOCs can have adverse effects on the health of employees and in many cases can negatively impact the environment.
While water-based mold release is the ideal solution from an environmental, health, and safety standpoint, it doesn’t work in every process. In the case of automotive seating there are typically two factors that determine this: dry time and active release component. As stated above, one of the active release components is typically a high-melt polymer that can protect the mold surface from the polyurethane while it is reacting. The melt point on these polymers can be well above 100C, making them difficult to emulsify into a water-based system. Secondly, if mold temperatures and dry time are not sufficient to evaporate the water, you will see foam collapse or “wax burn” on the finished part. Cosolvent mold release combines the benefits of a solvent-based system and the safety of a water-based release agent. With our proprietary processing equipment we are able to emulsify the ingredients needed to release these difficult polyurethane foam systems. Additionally, by including a small amount of solvent, we are able to reduce dry time making this product suitable for many automotive seating lines. While there still is a small percentage of VOCs included in our cosolvent mold release, it is significantly less than a traditional solvent based product.
In summary: our cosolvent mold release behaves in almost all regards like traditional solvent-based release agents and are cost comparable. In addition to the reduction in VOC’s, you’ll benefit from no longer having to handle the flammability hazard typically associated with solvent based mold releases.
Please give us a call so one of our trained field technicians can determine if the Hightower Products SA-Series is right for you (810) 714 1550.